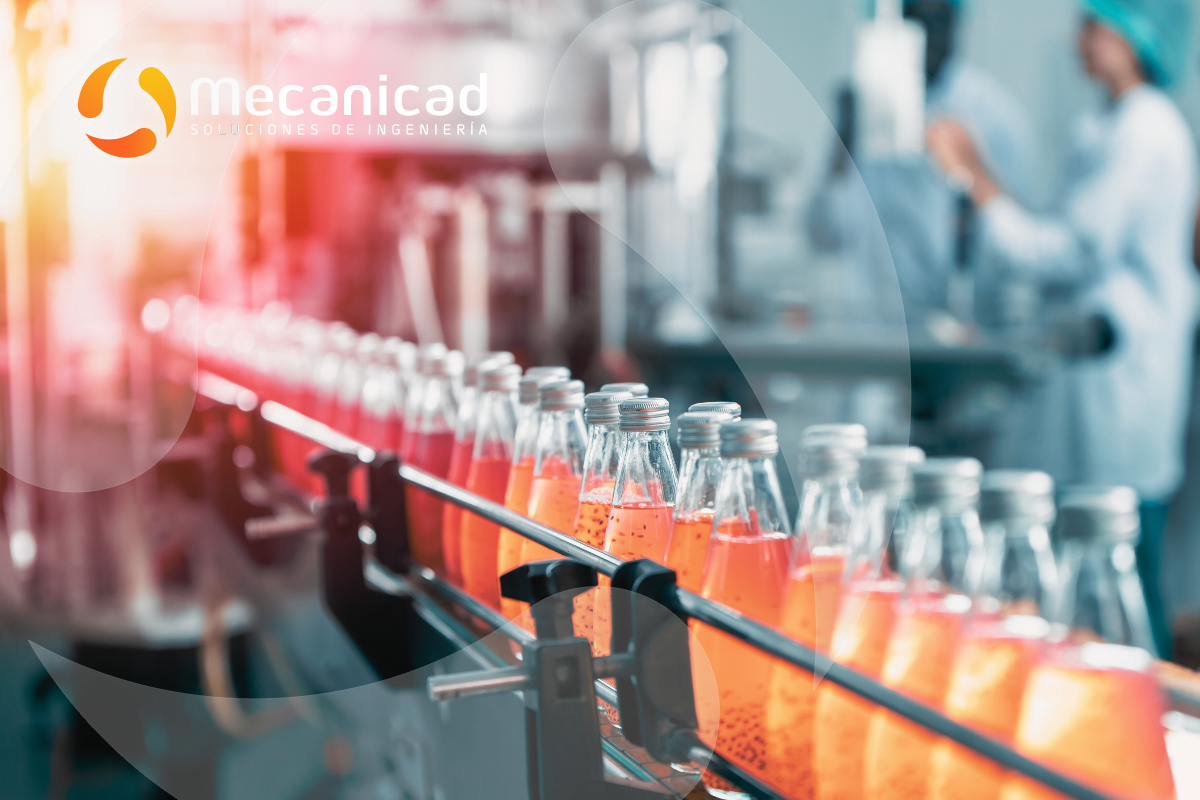
La optimización de los procesos de producción es una tarea esencial para mejorar la eficiencia, reducir costos y aumentar la competitividad de las empresas. En la fase de diagnóstico, se utilizan diversas herramientas y técnicas para identificar áreas de mejora y establecer una base sólida para la implementación de cambios efectivos. En este artículo, exploramos cuatro entregables clave de esta fase: el diagrama de mapa de procesos o VSM (Value Stream Mapping), el balanceo de línea, la identificación de tiempos de no valor agregado y el análisis de limitantes de productividad en el proceso.
La Optimización de los Procesos de Producción: Tu Camino al Éxito Empresarial
La optimización de los procesos de producción es una tarea esencial para mejorar la eficiencia, reducir costos y aumentar la calidad de los productos y servicios. En un entorno empresarial altamente competitivo, optimizar los procesos de producción no solo permite sobrevivir, sino también prosperar y destacarte entre tus competidores.
¿Por Qué es Importante Optimizar los Procesos de Producción?- Maximiza la Eficiencia: Al eliminar desperdicios y cuellos de botella, puedes asegurar que cada recurso se utilice de la manera más efectiva posible.
- Reduce Costos: Menos desperdicio significa menos gasto en materiales, energía y tiempo, lo que se traduce en un ahorro significativo para tu empresa.
- Aumenta la Calidad: Procesos más eficientes y controlados resultan en productos de mayor calidad y consistencia, lo que aumenta la satisfacción del cliente y la fidelidad a tu marca.
- Mejora la Satisfacción del Cliente: La entrega puntual y productos de alta calidad aseguran que tus clientes estén contentos y que vuelvan a confiar en tu empresa.
- Impulsa la Innovación: Un entorno de producción optimizado permite que los empleados se concentren en mejorar continuamente los procesos y productos, fomentando una cultura de innovación.
1. Diagrama de Mapa de Procesos o VSM (Value Stream Mapping)
El VSM es una herramienta visual que ayuda a mapear todos los pasos de un proceso de producción, desde la recepción de materias primas hasta la entrega del producto final al cliente. Este diagrama proporciona una visión detallada de cómo fluye el valor a través de la cadena de producción y dónde se generan los desperdicios.
- ¿Qué es el Mapa de Valor (VSM)?
El Mapa de Valor, conocido como VSM por sus siglas en inglés (Value Stream Mapping), es una herramienta visual poderosa que te permite ver todos los pasos de tus procesos de producción o servicios, desde el inicio hasta la entrega final al cliente. Este mapa te ayuda a identificar y eliminar los desperdicios, mejorar la eficiencia y aumentar la calidad.
- Propósito
El principal propósito del VSM es identificar oportunidades para eliminar actividades que no agregan valor y mejorar el flujo de valor en el proceso de producción. Al proporcionar una representación visual clara, facilita la comprensión y comunicación de los problemas y oportunidades entre los diferentes niveles de la organización.
- Beneficios
- Identificación de cuellos de botella y puntos de ineficiencia.
- Mejor comprensión del flujo de materiales e información.
- Facilita la toma de decisiones basadas en datos.
- ¿Por Qué Es Importante para Tu Negocio?
- Mejora de la Calidad: Al entender cada paso del proceso, puedes implementar mejoras que aseguren productos y servicios de alta calidad.
- Reducción de Costos: Eliminar los desperdicios significa menos costos operativos y mayores márgenes de beneficio.
- Aumento de la Satisfacción del Cliente: Procesos optimizados resultan en productos y servicios entregados a tiempo y con mayor calidad, lo que incrementa la satisfacción de tus clientes.
- ¿Cómo Funciona?
- Mapeo del Estado Actual: Primero, identificamos y documentamos cada paso de tus procesos actuales. Esto nos da una visión clara de dónde estamos.
- Análisis de Desperdicios: Analizamos el mapa para identificar áreas de desperdicio, cuellos de botella y otras ineficiencias.
- Diseño del Estado Futuro: Proponemos mejoras y diseñamos un proceso futuro más eficiente y optimizado.
- Implementación y Seguimiento: Trabajamos contigo para implementar las mejoras y hacemos seguimiento para asegurar que se mantenga la eficiencia.
2. Balanceo de Línea
El balanceo de línea es el proceso de distribuir las tareas de manera equitativa entre las diferentes estaciones de trabajo en una línea de producción. Esto se hace para asegurar que cada estación tenga una carga de trabajo similar y evitar tiempos de espera o inactividad.
- ¿Qué es el Balanceo de Línea?
El balanceo de línea es un proceso sistemático utilizado para distribuir de manera equitativa las tareas entre las diferentes estaciones de trabajo en una línea de producción. El objetivo principal es asegurar que cada estación tenga una carga de trabajo similar, evitando tiempos de espera o inactividad y logrando así un flujo de producción más uniforme y eficiente.
- ¿Cómo Funciona el Balanceo de Línea?
- Análisis de Tareas: Se descomponen todas las tareas necesarias en la línea de producción, identificando el tiempo y los recursos requeridos para cada una.
- Distribución Equitativa: Las tareas se distribuyen entre las estaciones de trabajo de manera que todas tengan una carga de trabajo equilibrada, evitando que algunas estaciones estén sobrecargadas mientras otras están inactivas.
- Ajuste y Optimización: Se realizan ajustes continuos para optimizar la asignación de tareas, considerando factores como la variabilidad en el tiempo de ciclo, la disponibilidad de recursos y la capacidad de la mano de obra.
- Implementación y Monitoreo: Las tareas equilibradas se implementan en la línea de producción, y se monitorea el desempeño para asegurar que se mantenga la eficiencia y se realicen ajustes cuando sea necesario.
- Propósito
El propósito del balanceo de línea es maximizar la eficiencia de la línea de producción, reducir el tiempo de ciclo y aumentar la productividad. Al equilibrar las cargas de trabajo, se minimizan las interrupciones y se mejora el flujo continuo del proceso.
- Beneficios
- Reducción de tiempos muertos y esperas.
- Incremento en la productividad y eficiencia.
- Mejora en la utilización de recursos y mano de obra.
- Propósito del Balanceo de Línea
El balanceo de línea busca maximizar la eficiencia de la línea de producción por medio de la identificación del equilibrar las cargas de trabajo, con este análisis se busca adaptar las mejores prácticas para reducir el tiempo de ciclo y aumentar la productividad. Esto no solo permite una visual de los hallazgos y oportunidades de mejora presentes en el flujo del proceso, sino que también permite identificar oportunidades de minimizar las interrupciones y maximiza la utilización de recursos.
3. Identificación de Tiempos de No Valor Agregado
Los tiempos de no valor agregado son aquellos que no contribuyen directamente al valor final del producto desde la perspectiva del cliente. Estos incluyen tiempos de espera, movimientos innecesarios, transporte de materiales y cualquier actividad que no transforme el producto.
- ¿Sabías que los Tiempos de No Valor Agregado Podrían Estar Costándote Miles?
En cualquier proceso de producción, uno de los mayores desafíos es identificar y eliminar los tiempos de no valor agregado (TNVA). Estos tiempos, aunque a menudo pasados por alto, pueden estar drenando la eficiencia de tu operación y aumentando innecesariamente tus costos. ¿Quieres saber cómo reconocerlos y eliminarlos para transformar tu negocio? Sigue leyendo.
- ¿Qué son los Tiempos de No Valor Agregado?
Los tiempos de no valor agregado son aquellas actividades o periodos durante los cuales no se agrega valor directo al producto o servicio desde la perspectiva del cliente. En términos sencillos, son todas aquellas pausas, retrasos y operaciones innecesarias que no contribuyen directamente a la creación de un producto o servicio que el cliente final valore.
- Ejemplos Comunes de TNVA:
- Esperas: Tiempo que los empleados, máquinas o materiales pasan inactivos esperando el siguiente paso del proceso.
- Transporte: Movimiento innecesario de materiales o productos dentro de la planta.
- Reprocesos: Corrección de errores o defectos que podrían haberse evitado.
- Inventarios Excesivos: Acumulación de materiales o productos que no se necesitan inmediatamente.
- Propósito
El propósito de identificar estos tiempos es eliminarlos o reducirlos al mínimo posible. Esto ayuda a aumentar la eficiencia general del proceso y reducir costos innecesarios.
- ¿Por Qué Son Importantes los TNVA?
Eliminando o reduciendo los tiempos de no valor agregado, puedes:
- Aumentar la Eficiencia: Mejorando el flujo de trabajo y reduciendo los cuellos de botella.
- Reducir Costos: Menos tiempo y recursos desperdiciados se traducen en menores costos operativos.
- Mejorar la Calidad: Menos interrupciones y movimientos innecesarios significan menos oportunidades para errores.
- Acelerar la Entrega: Un proceso más ágil permite entregar productos y servicios más rápido a los clientes.
- El Indicador de Tiempos de No Valor Agregado
Para gestionar y mejorar los TNVA, utilizamos un indicador específico que mide el porcentaje de tiempo total de producción dedicado a actividades de no valor agregado. Este indicador es crucial para:
- Diagnosticar Problemas: Identificar dónde se pierden más tiempo y recursos.
- Establecer Objetivos: Fijar metas de reducción de TNVA para mejorar la eficiencia.
- Monitorear Progresos: Medir los avances en la eliminación de TNVA a lo largo del tiempo.
- Tomar Decisiones Informadas: Utilizar datos precisos para implementar mejoras continuas.
- Beneficios
- Reducción de costos operativos.
- Mejora en la eficiencia del proceso.
- Aumento de la satisfacción del cliente al reducir tiempos de entrega.
- Nuestro equipo de expertos en eficiencia operacional está listo para trabajar contigo en la identificación y eliminación de TNVA en tu proceso de producción. Utilizamos herramientas avanzadas de análisis y técnicas probadas para asegurar que cada minuto de tu operación esté dedicado a agregar valor real.
4. Análisis de Limitantes de Productividad en el Proceso
- Descubre las Barreras Invisibles que Frenan la Productividad de tu Negocio
¿Te has preguntado alguna vez qué está frenando la productividad de tu empresa? En muchos casos, las limitantes de productividad no son evidentes a simple vista. Pero no te preocupes, estamos aquí para ayudarte a identificarlas y eliminarlas. Con nuestro análisis de limitantes de productividad, puedes transformar la eficiencia de tu operación y llevar tu negocio al siguiente nivel.
El análisis de limitantes de productividad, también conocido como análisis de cuellos de botella, se enfoca en identificar las restricciones que impiden que un proceso de producción alcance su máximo rendimiento. Estas limitantes pueden ser máquinas, recursos humanos, métodos de trabajo o cualquier otro factor que reduzca la capacidad productiva.
- ¿Qué son las Limitantes de Productividad?
Las limitantes de productividad, también conocidas como cuellos de botella y 8D (desperdicios MUDA), son obstáculos que impiden que el proceso de producción funcione a su máxima capacidad. Estas limitantes pueden surgir en cualquier parte de la cadena de producción y, si no se abordan, pueden generar:
- Tiempos de espera prolongados: Retrasos innecesarios que afectan la entrega de productos.
- Aumento de costos: Gasto adicional en recursos y horas extra.
- Desperdicio de materiales: Pérdidas de materias primas y productos finales.
- Reducción de calidad: Variaciones y defectos en los productos o sobreproducción: Producir más de lo necesario o antes de que se requiera, lo que genera inventarios innecesarios.
- Inventario: Exceso de materias primas, productos en proceso o productos terminados que no se están utilizando.
- Defectos: Productos que no cumplen con los estándares de calidad y requieren reprocesamiento o descarte.
- Procesamiento Excesivo: Realizar más trabajo del necesario en un producto debido a diseños deficientes o especificaciones poco claras.
- Movimiento: Movimientos innecesarios de personas dentro de la planta que no aportan valor al producto.
- Transporte: Desplazamientos innecesarios de materiales o productos que no añaden valor.
- Esperas: Tiempo en el que los empleados o las máquinas están inactivos esperando por materiales, información o equipos.
- Talento Infrautilizado: No aprovechar las habilidades y capacidades de los empleados al máximo.
- Propósito
El propósito de este análisis es encontrar y mitigar los factores que limitan la productividad. Al resolver estos problemas, se puede aumentar la capacidad y eficiencia del proceso de producción.
- Nuestro Enfoque en el Análisis de Limitantes
Realizamos un análisis exhaustivo de tu proceso de producción para identificar y abordar todas las limitantes de productividad, incluyendo los 8 desperdicios de MUDA. Nuestro enfoque incluye:
- Recolección de Datos: Utilizamos herramientas avanzadas para recopilar datos precisos sobre cada etapa de tu proceso.
- Análisis Detallado: Evaluamos los datos para identificar dónde y por qué se están produciendo las limitantes y los desperdicios.
- Identificación de Cuellos de Botella y Desperdicios: Localizamos los puntos críticos que ralentizan tu producción y generan desperdicios.
- Recomendaciones Prácticas: Proporcionamos soluciones efectivas y personalizadas para superar estas limitantes y reducir los desperdicios.
- Beneficios
- Incremento en la capacidad de producción.
- Reducción de tiempos de ciclo.
- Mejora en la eficiencia operativa.
- Beneficios de Nuestro Análisis
Al trabajar con nosotros, obtendrás:
- Mejora en la Eficiencia: Reducción significativa de tiempos de espera y aumento de la productividad.
- Optimización de Recursos: Mejor uso de materiales y mano de obra, reduciendo costos operativos.
- Incremento de la Calidad: Producción más consistente y de mayor calidad.
- Aceleración de Tiempos de Entrega: Capacidad para cumplir con los plazos de entrega de manera más confiable.
- Reducción de Desperdicios: Minimización de los 8 desperdicios de MUDA, optimizando el flujo de trabajo y recursos.
La fase de diagnóstico en un servicio de optimización de procesos de producción es crucial para identificar áreas de mejora y establecer una base sólida para la implementación de cambios efectivos. Los cuatro entregables clave discutidos - el diagrama de mapa de procesos o VSM, el balanceo de línea, la identificación de tiempos de no valor agregado y el análisis de limitantes de productividad - proporcionan una comprensión detallada y una visión estratégica de cómo mejorar los procesos de producción. Al abordar estas áreas, las empresas pueden aumentar su eficiencia, reducir costos y mejorar su competitividad en el mercado.
También te puede interesar: ¿Qué es y cómo funciona el diseño de plantas industriales?
Deja tus comentarios aquí